Hi-vis reflective safety vests play an indispensable role in ensuring the safety and visibility of workers across various industries, such as construction, road works, and emergency response. The meticulous manufacturing process of safety vests ensures their functionality and safety, crucial for hazardous work environments. This article introduces the comprehensive manufacturing process of safety vests, underscoring their pivotal role in enhancing worker visibility and safety.
Design and Development
The journey of creating a safety vest begins at the drawing board. Once an order is confirmed, a dedicated in-house design team leverages advanced software to draft a prototype of the vest. This prototype encompasses essential elements such as craftsmanship, color, materials, and packaging methods, ensuring that every detail is meticulously planned.
A comprehensive technical file is crafted alongside the prototype. This document serves as the blueprint for the production process, ensuring uniformity and coherence across various production teams. It meticulously details every aspect of the vest's design, serving as a guideline for seamless manufacturing.
Crucially, the design phase incorporates adherence to prevalent safety standards such as ANSI/ISEA, which stipulate stringent requirements for visibility, color, and reflective materials. This compliance is non-negotiable, as it guarantees that the vests meet the exacting safety demands of diverse work environments.
Once the initial design is drafted, it is reviewed by various teams. This collaborative feedback mechanism is vital for refining the vest, enhancing its functionality, and ensuring it meets the dual demands of safety and user comfort. This stage is not merely about meeting standards but also about innovating to address the practical and comfort needs of the end-users.
Through an exhaustive and collaborative design process, manufacturers ensure that the safety vests are not only compliant with safety regulations but are also tailored to enhance wearer comfort and functionality in high-risk environments.
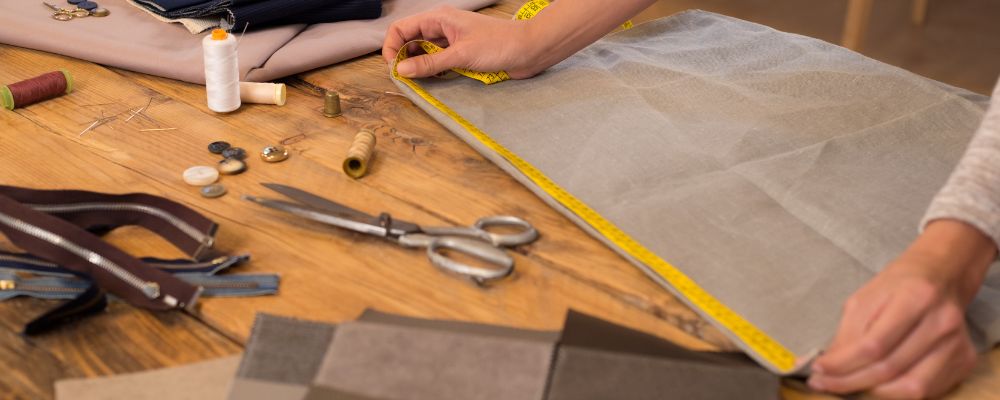
Sourcing Quality Materials
The integrity of safety vests hinges significantly on the quality of the materials used. The fabrics must be robust, comfortable, and capable of accommodating essential safety features like reflective and fluorescent materials. Predominantly, materials such as polyester and nylon are chosen for their durability and adaptability to various environmental conditions.
To fulfill rigorous safety standards like ANSI/ISEA, the vests are equipped with reflective tapes and vivid fluorescent colors to ensure high visibility, particularly in low-light conditions. The materials undergo stringent testing to verify compliance with these standards, often accompanied by certifications from recognized accrediting bodies.
Selecting the right material suppliers is a critical decision. Establishing long-term partnerships with trusted suppliers ensures a consistent supply of high-quality materials, which can also be cost-effective over time. Moreover, there is an increasing move towards incorporating sustainable materials like recycled polyester, which supports environmental sustainability without compromising on safety.
By prioritizing the procurement of high-quality, compliant, and sustainable materials, manufacturers of safety vests ensure their products are reliable and effective in protecting wearers.
Rigorous Material Inspection
The inspection of raw materials marks a fundamental phase in the safety vest manufacturing process. This stage is critical to ensuring that the final product complies with stringent safety standards and fulfills customer expectations. Upon their arrival, materials are meticulously inspected to verify their conformity with the specified quality standards, including assessments of color, texture, and overall durability.
Further, the materials undergo detailed testing for their reflective capabilities and resilience under diverse conditions. These tests include stress tests, assessments of colorfastness, and verifications that the reflective materials fulfill visibility standards essential for safety. Documentation for each batch of materials includes detailed records of the supplier, batch number, and test results, facilitating traceability and accountability in case any discrepancies arise.
Human expertise is invaluable in this phase; skilled inspectors, equipped with deep knowledge and an eye for detail, are essential. They are adept at identifying subtle defects that automated systems might overlook, such as minor flaws in fabric weave or inconsistencies in the application of reflective materials.
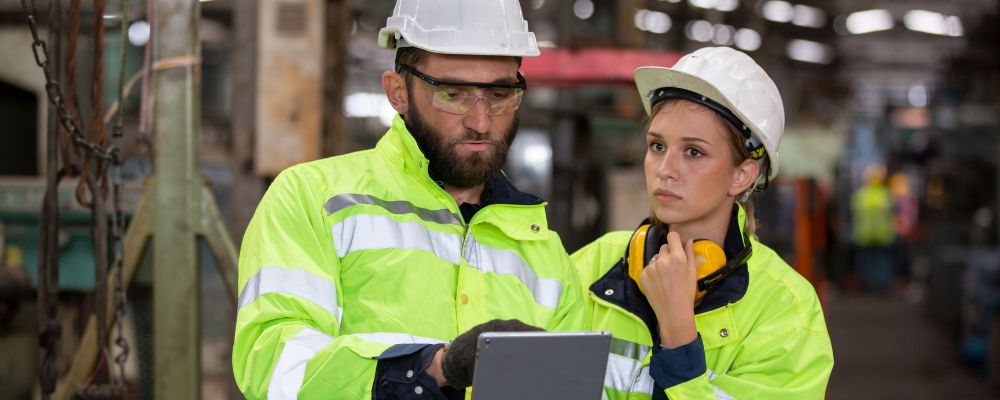
Precise Fabric Cutting
Following material inspection, the precise cutting of fabric is the next crucial step in the manufacturing of safety vests. This stage relies on exact patterns and templates, which were developed during the design phase, to ensure that each fabric piece precisely matches the required dimensions and shapes. Such accuracy is vital for the functionality and fit of the final product.
Advanced digital cutting machines, programmed with specific design specifications, are employed to achieve high efficiency and accuracy. These machines ensure consistent cuts, minimize material waste, and support sustainable manufacturing practices. Prior to cutting, an initial check of the fabrics ensures they are free from any defects, as imperfections could undermine the integrity and safety efficacy of the finished vests. Post-cut, another round of inspections confirms that all pieces align with the required specifications.
Skilled Sewing and Assembly
The assembly and sewing of safety vests represent the culmination of the manufacturing process, where all prepared materials are stitched together to form a functional and durable safety garment. High-grade industrial sewing machines, designed for heavy-duty tasks, handle robust materials like thick polyester and reflective strips.
Specialized sewing techniques are employed to ensure that all components are securely attached and able to endure rigorous use. This includes reinforced stitching at stress points and seamless integration of reflective materials to maintain the vest's integrity and visibility. Continuous quality checks during the sewing process are paramount; these include inspections of stitching quality, alignment of parts, and the functionality of added features like zippers and Velcro.
The precision required in the sewing process demands a highly skilled workforce. Sewers must be adept at handling complex patterns and durable materials to ensure that each vest is crafted to perfection. Efficiency in the sewing lines is optimized by assigning specific tasks to different groups and integrating automation for tasks such as label attachment or straight seams sewing, which speeds up production without sacrificing quality.

Real-Time Online Inspection
Online inspection is a pivotal quality control stage in the manufacturing process of safety vests. It ensures that each vest adheres to stringent safety and durability standards even before it reaches the final inspection and packaging phases. Throughout the sewing and assembly process, vests are subjected to continuous, real-time monitoring. This monitoring involves advanced technologies, including high-resolution cameras and automated defect detection systems, strategically placed along the production line. These technologies are instrumental in identifying any discrepancies, such as misaligned stitches or incorrect placement of reflective materials.
However, technology alone isn’t enough. Well-trained inspectors play a crucial role in this phase, bringing their expertise to quickly rectify issues that automated systems might miss. Regular training programs keep the inspection teams adept at utilizing the latest quality control technologies and techniques, ensuring they remain proficient with new tools and compliant with evolving safety standards. This early detection of defects not only maintains high product quality but also boosts manufacturing efficiency by reducing the need for reworks.

Final Inspection and Quality Control
The final inspection and quality control phase is the definitive line of defense in the safety vest manufacturing process, ensuring that every vest meets all required standards and specifications before dispatch. At this stage, each vest undergoes a comprehensive review, checking for any defects in materials, craftsmanship, and adherence to design specifications.
Inspectors utilize detailed checklists, meticulously covering every aspect of the vest’s design and construction. This process ensures consistency and thoroughness in quality assurance across all products. The findings from these inspections are systematically documented, creating a traceable quality assurance record that is vital for addressing any customer concerns post-purchase and for driving continuous improvement in manufacturing processes.
To augment the precision of manual inspections, technologies such as 3D scanning and automated defect recognition systems are employed. These technologies help in spotting even the slightest inconsistencies and flaws that might elude the human eye. Highly skilled personnel, proficient in both the technical aspects of safety vest production and the latest inspection techniques, carry out this critical final stage of quality assurance.
Conclusion
Safety vests are more than mere protective gear for the safety and well-being of workers. Providing high visibility in hazardous situations, these vests significantly reduce the risk of accidents and ensure compliance with safety regulations. The manufacturing process of safety vests combines quality, functionality, and safety, ensuring that each vest meets rigorous standards and thoughtful design. This meticulous approach guaranteed the role of safety vests as essential tools in promoting safer work environments.
FAQs
What are the key stages in the manufacturing process of safety vests?
The manufacturing process of safety vests includes several key stages: design and prototyping, material sourcing, fabric cutting, sewing, online and final inspections, and finally, packaging and delivery. Each stage is crucial to ensure the vests meet safety standards and are durable and functional for use in various industries.
Why is high visibility important for safety vests?
High visibility is crucial for safety vests because it ensures that the wearer is easily seen in different environments, particularly in low-light conditions or where there are numerous visual distractions. This visibility is vital for preventing accidents, especially around moving vehicles or machinery.
What roles do inspections play in the manufacturing process of safety vests?
Inspections are critical throughout the manufacturing process of safety vests. They ensure that each vest meets predefined quality and safety standards. This includes checking the materials, assembly, stitching, and final appearance of the vests. Inspections help identify and rectify any defects before the vests reach the end-user, ensuring high quality and safety.