In today's safety-conscious world, safety protective work gloves have emerged as indispensable tools for protecting workers' hands across a wide range of industries. From construction sites to chemical handling facilities, these essential garments play a crucial role in safeguarding employees from a myriad of hazards. However, navigating the complexities surrounding work glove classifications and standards can be a daunting task.
This comprehensive guide aims to introduce the classification and safety standards of work gloves, serving as a roadmap for safety managers, professionals, and anyone seeking a deeper understanding of these critical protective garments.
Diverse Applications of Work Gloves
Work gloves find applications across numerous industries, each with unique hazards and requirements. Their versatility in providing protection makes them an indispensable part of workplace safety.
Construction and Carpentry: Construction and utility gloves shield workers from splinters, cuts, and abrasions caused by rough materials and tools.
Chemical Handling: Specialized gloves offer resistance against hazardous substances and corrosive liquids, safeguarding workers from exposure.
Automotive: Mechanics and technicians rely on gloves to protect against cuts from metal parts and burns from hot engines.
Agriculture and Gardening: Gloves prevent exposure to thorns, sharp tools, and pesticides, ensuring worker safety during manual labor.
Healthcare: Acting as barriers against biological hazards, gloves prevent the transmission of infectious diseases between patients and healthcare professionals.
Food Service: Gloves maintain hygiene standards by preventing direct hand contact with food, reducing the risk of contamination.
Electrical Work: Insulated gloves protect electrical workers from potential shocks and burns when working with live wires or equipment.

This wide range of applications highlights the vital role safety protective work gloves play in ensuring the safety and well-being of workers across various industries, making them an essential component of personal protective equipment (PPE) strategies.
Glove Standards: ANSI/ISEA and EN
Understanding glove standards is crucial for selecting the right protective safety glove for specific hazards. Two prominent standards, ANSI/ISEA 105 and EN 388, provide rigorous frameworks for evaluating gloves' resistance to mechanical risks, including cuts, punctures, and abrasions.
ANSI/ISEA 105 (U.S. Standard)
The American National Standards Institute (ANSI) and the International Safety Equipment Association (ISEA) established ANSI/ISEA 105. This standard evaluates cut, puncture, and abrasion resistance using specific testing methods. For cut resistance, a tomodynamometer (TDM) machine measures the force required for a blade to cut through the glove material. Scores range from A1 (lowest protection) to A9 (highest protection), providing a clear distinction between levels of cut resistance.
EN 388 (EU Standard)
The European EN 388 standard also tests for protection against mechanical hazards, including cuts, punctures, and abrasions. However, it uses slightly different methods. Cut resistance testing involves two methods: the Coupe Test and ISO 13997. The Coupe Test assigns scores from 1 to 5 based on resistance to a rotating blade. Materials with high resistance undergo further testing using the ISO 13997 method with the TDM-100 machine, similar to ANSI's approach. This provides a letter score from A to F for accurate measurement of high-cut-resistant materials.
Recent Updates
In recent years, both ANSI/ISEA and EN standards have undergone revisions to enhance accuracy and achieve closer alignment.
EN 420 and ANSI/ISEA 138-2019 expanded its scope to include impact resistance testing for work gloves, specifically focusing on dorsal protection. This update addresses the need for evaluating the gloves' ability to protect the back of the hand from impact hazards, further enhancing worker safety.
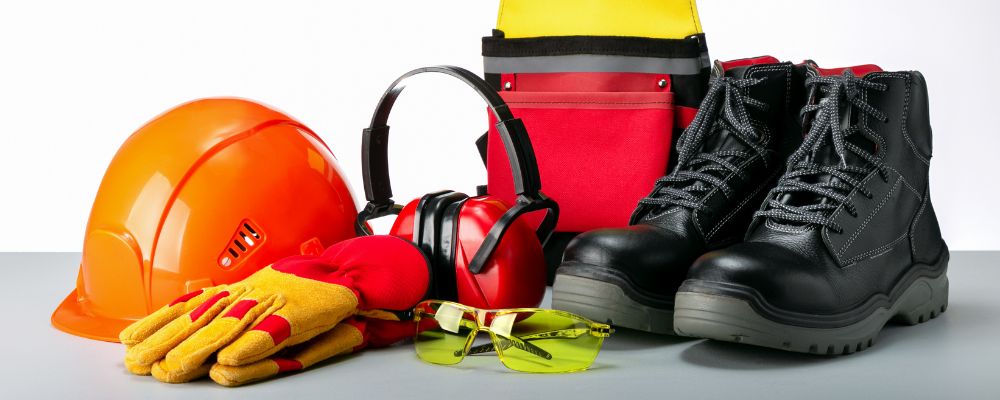
Categories of Work Gloves
Work gloves are categorized based on the level of risk they protect against, as defined by European regulations.
Category I: gloves are suitable for minimal risks. They are not subjected to EN testing like EN 388 for mechanical resistance and are generally used in low-risk environments such as product assembly or stock handling. For instance, cotton glove liners fall under this category, providing a basic level of protection and comfort for tasks that require manual dexterity without significant risk of injury.
Category II: gloves are intended for intermediate risks and must conform to specific EN standards such as EN388, which covers mechanical protection. These gloves offer protection against a broader range of hazards and are suitable for various applications, including construction or automotive work. They are tested and certified by accredited institutes to ensure they provide the stated level of protection.
Category III: gloves provide the highest level of protection against risks that can cause very serious consequences, including death or irreversible harm. They are rigorously tested and must be certified by a Notified Body for both type and production control. Gloves in this category protect against severe hazards, including chemicals and extreme temperatures, and are marked with pictograms indicating their protective properties.
These gloves are rigorously tested and certified by Notified Bodies, ensuring they meet stringent safety requirements for protection against hazards such as chemicals and extreme temperatures.
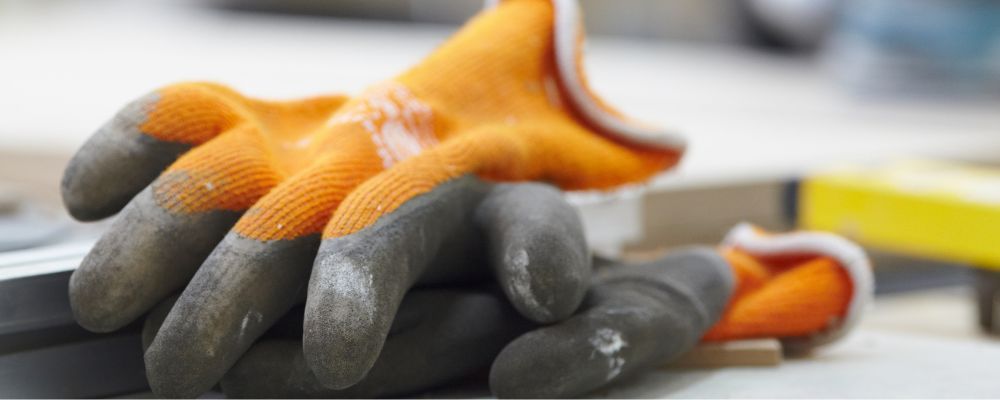
Choosing the Right Work Gloves
Choosing the appropriate work gloves is a critical decision that involves several key considerations:
Understanding Hand Hazards: Assess the working environment and identify potential hand hazards, such as cuts, abrasions, chemical exposure, and temperature extremes.
Glove Materials: Evaluate different glove materials and their respective protective capabilities, flexibility, and comfort. Materials like latex, nitrile, and leather offer varying levels of protection and dexterity.
Compliance with Safety Standards: Familiarize yourself with relevant safety standards, such as ANSI/ISEA and EN, which classify gloves based on their protective capabilities. Standards like ANSI/ISEA 138-2019 and EN 420 provide guidance on impact resistance and general requirements for glove selection.
Job-Hazard Analysis: Perform a thorough job-hazard analysis to match glove materials and standards to the identified risks, ensuring you choose gloves with the right combination of protection levels for the specific task.
Proper Sizing: Incorrectly sized gloves can lead to discomfort, reduced dexterity, and increased risk of injury. Measure the hands of your workers to ensure a proper fit, and maintain a well-stocked inventory of sizes to accommodate everyone.
By following these guidelines, you can ensure that workers are equipped with the necessary hand protection to safely and efficiently perform their tasks, fostering a culture of safety and productivity in the workplace.
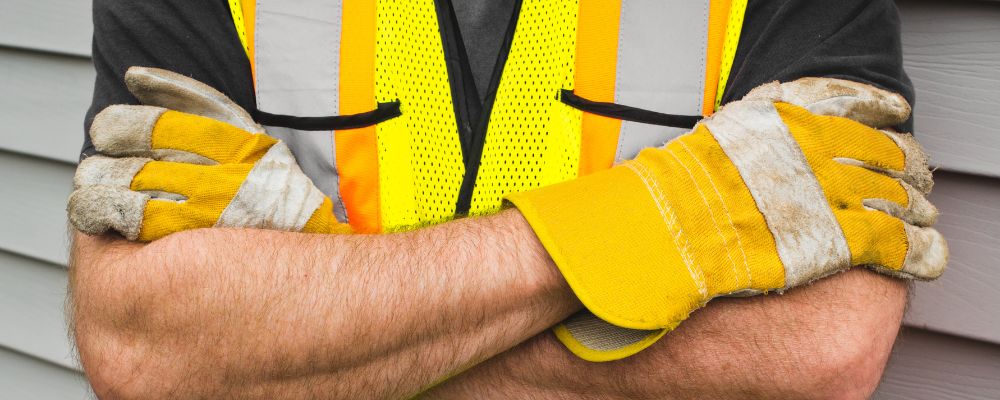
Conclusion
Work gloves are more than just a basic protective layer; they are essential tools that safeguard workers from a wide array of occupational hazards. Their diverse applications across industries underscore the importance of selecting the right type of glove, a choice that hinges on a thorough understanding of specific risks, materials, and standards.
By embracing the guidance provided by standards like ANSI/ISEA and EN, and following best practices for glove selection, employers and workers alike can foster a safety-conscious and efficient workforce.
FAQs
What are the main classifications of work gloves and what do they mean?
Work gloves are classified based on the level of protection they offer against specific hazards. There are three main categories:
- Category I: Gloves in this category offer basic protection against minimal risks. They are suitable for tasks where there is a low risk of injury.
- Category II: These gloves are designed to protect against intermediate risks. They must meet specific EN standards, such as EN388 for mechanical protection, and are used in more hazardous work environments.
- Category III: Gloves falling into this category offer the highest level of protection against risks that can cause very serious consequences, such as chemicals or extreme temperatures. They undergo rigorous testing and certification processes.
How do ANSI/ISEA and EN standards for work gloves differ?
ANSI/ISEA and EN standards both provide frameworks for testing and classifying work gloves based on their protective capabilities. The main difference lies in their geographic application and specific testing methods. ANSI/ISEA standards are predominantly used in the United States, while EN standards are followed in European countries. Both set of standards evaluate gloves on aspects like cut, puncture, abrasion resistance, but they use different testing protocols and scoring systems.
Can work gloves be washed and reused, or are they designed for single use?
The reusability of work gloves depends on their material and design. Some gloves, especially those designed for chemical resistance or heavy-duty protection, can be cleaned and reused multiple times. However, gloves meant for single-use must be disposed of after use to prevent contamination. Always refer to the manufacturer’s instructions for care and maintenance to ensure the gloves maintain their protective qualities.